Cast Underlayment
Cast Underlayment, often referred to generically as “gypcrete,” Maxxon Corp’s registered trademark name, has been used for the leveling of rough and uneven floors, for wood floor systems requiring fire ratings and acoustic control, and as the encapsulation material for in-floor radiant heating. The increased material strengths available today, along with ever-increasing competition, have led to the manufacture of more durable products and an increased use of cast underlayments since the 1990s. The application of cement underlayment is similar to traditional techniques for casting concrete. Cement underlayment (non-structural) can be added over existing concrete or timber floors, both interior and exterior, provided that the substrate is structurally sound.
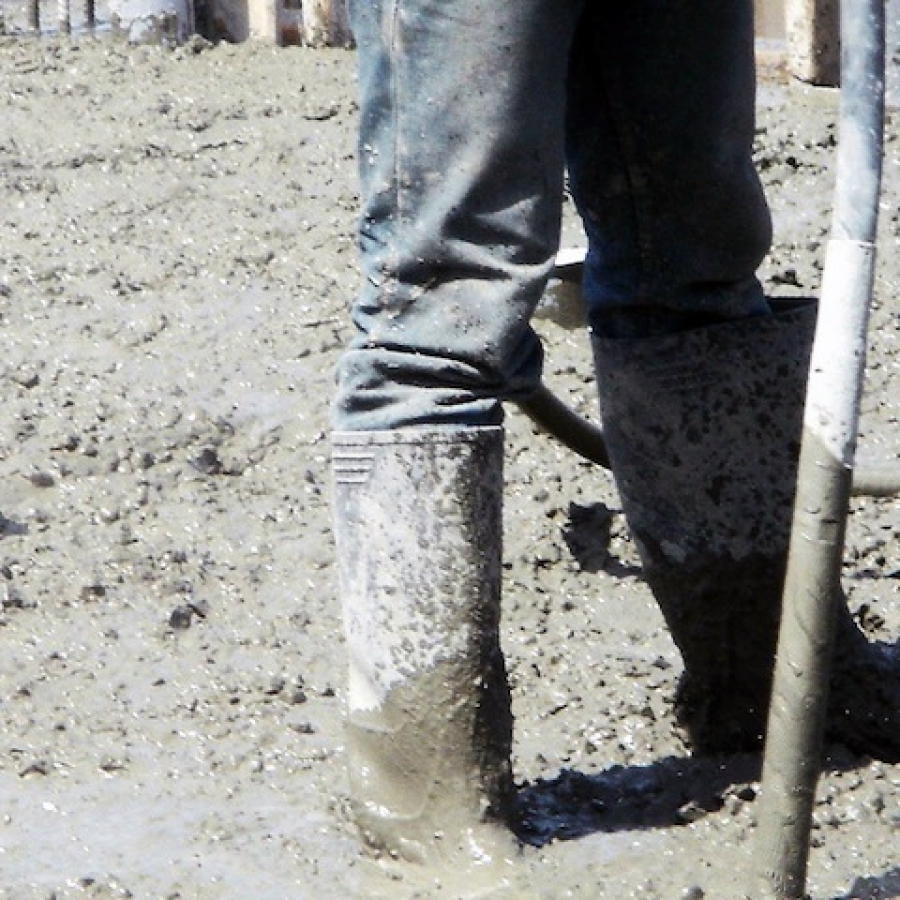
Topic Summary
When concrete underlayment is applied over rough, uneven, and warped surfaces, it creates a smooth, flat floor that is capable of withstanding the point loads found in office and light industrial buildings.
A variety of underlayments are commercially available with many of them based on hydraulic cements containing limestone, certain clay minerals, and gypsum (calcium sulfate dehydrate). These cements harden and set as a result of chemical reactions with water. Materials are designed to come up to required strengths with depths of as little as 1/4" thickness and are typically not used when the total required depth exceeds 4". Most cast underlayment products are not intended to be left exposed, but are to be covered with a finish flooring material.
Methods and Materials
When using cast cement underlayment, the surface to be coated should be thoroughly damp or, if this is not possible, a bonding agent should be applied. The cement is mixed in a slow speed mixer before being deposited into formwork, the side forms of which are coated with a release agent. The underlayment is then spread, consolidated, leveled, finished, and cured. During the curing process, which requires 3-4 hours at 70°F, the cement layer can be covered with wet burlap, or a curing compound can be applied.
Gypsum concrete underlayments produce flat, crack-free layers, are easily installed, and set quickly. Polymer-modified, cement-based underlayment materials are self-leveling and have good flow characteristics, making them attractive for covering unfinished interior floors for subsequent application of tile, marble, wood, or carpet. Materials must comply with ASTM C 317 and ASTM C 956.
Environmental Considerations
For the underlayment to set rapidly, the temperature of the air, substrate, liquids, hardener and powder components should be maintained between 60° and 80°F during mixing, placing and curing. Monolithic substrates should be maintained between 65° and 80°F for 48 hours prior to placing the cement underlayment. The application is not recommended if the temperature is above 80°F or below 35°F. Application in direct sunlight can lead to blisters forming on the surface of the cement underlayment, due to the expansion of trapped air or the presence of water. Substrates that have been exposed to sunshine for a period of time should be shaded for at least 24 hours before applying the cement underlayment.
Most manufacturers have underlayment materials that will work in more extreme weather conditions. However, these usually are at a premium cost.
Design Basics
The design is based on the following:
- The substrate on which the underlayment is to be applied
- The weight that the substrate and its supporting system can carry
- The strength in deflection of the substrate; 1/360 deflection is the recommended maximum
- The point load and impact load requirements for the end use
- The minimum and maximum thickness allowed
- The required fire rating
- The acoustic requirements
- The rate of drying required
- Is in-floor radiant heat required?
Preparations
The substrate should be structurally sound and its surface free of dirt and debris. Oil and grease stains or other chemical stains must be removed and, if necessary, the surface should be either hydroblasted or sandblasted to remove a thin top layer.
Applications and Installations
Expansion joints in the concrete floor should continue through the underlayment at the same width. Underlayment is applied by pumping the underlayment mix through a hose and applicator valve and nozzle on or near the floor. The placement is from the furthest point to the nearest point with adequate speed to avoid having edges begin to set. Although many underlayments are self-leveling, a screed is used to pull excess material to the open areas. Lasers are often used to assure a consistent elevation.
Surfaces should be protected with high-traffic areas covered with plywood until the finish flooring is applied.
Other Considerations
Fast setting underlayments are available with initial set times as low as 1-1/2 hour. Traffic bearing underlayments with compressive strengths exceeding 6,000 psi provide a light traffic bearing surface in as little as 24 hours. Underlayments installed over wood substrates may require reinforcing mesh.
With a moist material being applied to organic substrates or beside materials with organic content the growth of mold and mildew is possible. Concrete Floors and Moisture by PCA addresses these and other concerns and is available at the ACI website.
Standards and Codes
- The International Building Code Chapter 19 Section 1915 by ICC states the minimum design standards for Reinforced Gypsum Concrete.
- Reinforced concrete shall comply with ACI 318 and ACI 318, Section 3.5.
- American Concrete Institute ACI 305 Hot Weather Placement of Concrete.
- ACI 306 Cold Weather Placement of Concrete.
03 54 00Cast Cement Underlayment
Often referred to as “gypcrete”, Maxxon Corp’s registered trademark name, cement underlayment has been used for leveling of space, rough, uneven floors and wallsor for wood floor systems requiring fire ratings and acoustic control, or as the encapsulation material for in-floor radiant heating. can be covered with a cement underlayment to give a smooth, flat surface The increasing material strengths and increasing competition has provided more durable products and has lead to the increased useof underlayments since the 1990s. The application of the several varieties of cement underlayment is similar to the traditional techniques for casting concrete. Cement underlayment (non-structural) can be added to existing concrete or timber floors, both interior and exterior, provided that the substrate is structurally sound.
Description and Uses
Underlayment iscan be applied over rough, uneven and warped surfaces to create a smooth, flat floor that is capable of withstanding the point loads found in office and light industrial buildings.
A variety of underlayments are commercially available, many based on hydraulic Portland cements containing limestone, certain clay minerals and gypsum (calcium sulfate dehydrate). These cements harden and set as a result of chemical reactions with water. Although thicknesses can range from ¼” to 4”, the average thickness is 1 ½ “.
This cement-based product can be applied to vertical and overhead surfaces, but layers over 0.5 inches thick should be reinforced and anchored. Vertical applications are normally for fireproofing. A variety of underlayments are commercially available, many based on hydraulic Portland cements containing limestone, certain clay minerals and gypsum (calcium sulfate dehydrate). These cements harden and set as a result of chemical reactions with water.
Methods and Materials
In general, Mmuch of the practice used to place concrete* (internal link to “Concrete Placement”) is used to cast cement underlayment. The surface to be coated should be thoroughly damp and, if this is not possible, a bonding agent should be applied. The cement is mixed in a slow speed mixer before being deposited into formwork* (internal link to “Cast-in-Place Structural Concrete Forming”), the side forms of which are coated with a release agent. The underlayment cement is then spread, consolidated, leveled, finished* (internal link to “Concrete Finishing”) and cured (internal link to “Concrete Curing”)., During the curing process, which requires 3-4 hours at 70°F, the cement layer can be covered with wet burlap or a curing compound applied.
Gypsum concretes produce flat, crack-free layers, are easily installed and set quickly. Polymer modified ,cementmodified, cement-based underlayment materials are self-levellingleveling and have good flow characteristics, making them attractive for covering unfinished, interior floors for subsequent application of tile, marble, wood or carpet.
The material shall comply with ASTM C 317 and ASTM C 956.
A wide variety of products/materials are available from various manufacturers at the following websites:
http://www.hackerindustries.com/products.htm
http://www.rapidfloor.com/floor_products/index.shtml
http://www.symons.com/products/brochure/chemical/11fl.htm
Environmental Considerations
For the underlayment to set rapidly, the temperature of the air, substrate, liquids, hardener and powder components should be maintained between 60° and 80°F during mixing, placing and curing. Monolithic substrates should be maintained between 65° and 80°F for 48 hours prior to placing the cement underlayment. The application is not recommended if the temperature is above 80°F or below 35°F. Application in direct sunlight can lead to blisters forming on the surface of the cement underlayment, due to expansion of trapped air or the presence of water. Substrates that have been exposed to sunshine for a period of timeof time should bestored in a shadedareafor at least 24 hours before applying the cement underlayment.
Most manufacturers have underlayment materials that will work in more extreme weather conditions. However, they usually are at a premium cost.
Design/Basics
The design is based on the following:
The substrate on which the underlayment is to be applied
The weight that the substrate and its supporting system can carry
The strength in deflection of the substrate; 1/360 deflection is the recommended
maximum.
The point load and impact load requirements for the end use
The minimum and maximum thickness allowed
The required fire rating
The acoustic requirements
The rate of drying required
Is in-floor radiant heat required?
The Maxxom Corp. and Hacker Industries provide charts for the selection and proper choice of their underlayment products at
http://www.rapidfloor.com/product_selection_guide/index.shtml
http://www.hackerindustries.com/productschart.htm
The benefits of Underlayment are shown on Hacker Industry website at
http://www.hackerindustries.com/concrete-floor-underlayments.shtml
Preparations
The substrate should be structurally sound and its’ surface free of dirt and debris. Oil and greased stains or other chemical stains must be removed and, if necessary the surface should be either hydro blasted or sandblasted to remove a thin, top layer.
Applications and Installations
Expansion joints in the concrete floor should continue through the underlayment at the same width.
Underlayment is applied by pumping the underlayment mix thru a hose and applicator valve and nozzle on or near the floor. The placement is from the furthest point to the nearest point with adequate speed to avoid any edges beginning to set. Although many underlayments are self-leveling, a screed is used to pull excess material to the open areas. Lasers are often used to assure a consistent elevation.
The proper drying conditions for most underlayments are summarized at http://www.hackerindustries.com/dryingconditions.pdf
Surfaces should be protected with high traffic areas covered with plywood until the finish flooring is applied.
Other Considerations
Fast setting underlayments are available with initial set times as low as 1½ hour.
Traffic bearing underlayments with compressive strengths exceeding 6,000 psi provide light traffic bearing surface in as little as 24 hours.
Hacker Industries provides a Guideline for Installing Finish Floor Coverings at:
http://www.hackerindustries.com/true-screed.htm
With a moist material being applied to organic substrates or beside materials with organic material the growth of mold and mildew is possible. Concrete Floors and Moisture by PCA addresses these and other concerns and is available at the ACI website: http://www.concrete.org/bookstorenet/ProductDetail.aspx?itemid=CFM
Standards and CodesAmerican Concrete Institute ACI 305 Hot Weather Placement of Concrete
ACI 306 Cold Weather Placement of Concrete
The International Building Code Chapter 19 Section 1915 by ICC states the minimum design standards for Reinforced Gypsum Concrete.
Reinforced concrete shall comply with ACI 318 and ACI 318, Section 3.5.
American Concrete Institute ACI 305 Hot Weather Placement of Concrete*
ACI 306 Cold Weather Placement of Concrete*
Costs
The Cost Data* provides a unit pricing for installed underlayment in both standard and high strength products.
Cost estimating formulas are provided by the Smalley & Company at
http://www.smalleyandcompany.com/conestimate.html
The following national cost estimating books provide material and labor costs:
RS Means Building Construction Cost Data
Sweets Facility Cost Guide
National Concrete and Masonry Estimator
Related Information
Bob Harris Guide to Concrete Overlays and Toppings by PCA is a series of guides that includes a section on underlayments.
Floor coverings can be applied to some underlayments in as little as 15 hours. USG discusses its full line of self-leveling cement at http://www.levelrock.com/
USG’s outline underlayment information at http://www.gypsumsolutions.com/
The AEC INFO website provides information of hydraulic cement underlayments at http://www.aecinfo.com/1/category/11/46/70/category_1.html
The Gypsum Today promotes the use of gypsum products. Specific information about underlayments are at http://www.gypsumtoday.com/floors.shtml
Information on the use of underlayments with radiant heat is available from the Radiant Panel Association at http://www.radiantpanelassociation.org/i4a/pages/index.cfm?pageid=1
References
Website, Sauereisen, Pittsburgh, PA
Retrieved August 4, 2007 from
http://www.sauereisen.com/pdf/f_120FS.pdf
Website, Symons by Dayton Superior Corporation, Dayton, OH
Retrieved August 4, 2007 from
http://www.symons.com/products/brochure/chemical/11fl.htm
Gypsum Cement Underlayment
Website, Hacker Industries Incorporated, Newport Beach, CA
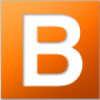
Buildipedia Staff
The Buildipedia research and writing staff consists of dozens of experienced professionals from many sectors of the industry, including architects, designers, contractors, and engineers.
Website: buildipedia.com/