Resilient Flooring
Resilient flooring refers to a type of material that has "give" as weight compresses its surface, and "return" (to its original surface profile) after the weight has been removed. Common types of resilient flooring are made from materials like rubber, linoleum, cork, asphalt, and vinyl.
Linoleum is made from natural, raw materials, and is the environnmentally-conscious material of choice. Linseed oil, which comes from the flax plant, is its primary ingredient. Other ingredients include wood or cork powder, resins, and ground limestone. Mineral pigments provide the rich colors. The ingredients are mixed together, and then rolled out between two cylinders onto a natural backing made from jute. The linoleum is cured in ovens for 14 to 21 days. Some manufacturers bond a high performance coating to the surface to improve the floor’s ability to resist stains and scratches, and to make cleaning easier. Sheet linoleum is available in many thicknesses, but 2.5 mm or thicker is suitable for residential use. It is sold in 6’ 7” width. Linoleum tile is also available, but it is more prone to warping and curled edges.
New linoleum sometimes has a yellow cast on the surface, called a "drying room film," that is a natural effect created by the floor's composition. This film will dissipate when the floor is exposed to natural or artificial light. Make sure you expose linoleum samples to light for several hours before making your final design and color choice.
In 1904, the first cork floor tile was introduced, and it became very popular. Cork remained a popular type of resilient flooring through the 1920s. Cork flooring is environmentally friendly and cork is considered a renewable and sustainable natural resource. These floors can be a bit expensive, with their installed cost per square foot being close to that of a good quality ceramic tile floor. However, they are definitely worth the cost when used in smaller areas such as a kitchen, den or dining room. The same cellular structure that makes the floor comfortable to walk on also reduces noise and vibration. Unlike hard materials such as tile, wood or vinyl, cork is quiet and reduces impact noise (such as something dropping onto the floor). Cork now comes in a variety of colors, patterns and textures. Some companies mix rubber with cork to provide a special texture; some others are known for producing cork with very vibrant colors. Some patterns resemble plank boards.
Glue-down installation results in lower material costs, but much higher installation costs. It is also more difficult to repair a glued tile as opposed to a floating floor installation. Furthermore, glue-down floors can only be applied over a smooth, clean substrate. Floating floor installations are more common and are a preferred method of installation. These cork planks come with a specially designed edge that interlocks with the adjacent panels, similar to tongue and grooved edges in wood. Some manufacturers' floating floor products can be installed over most hard surfaces, such as vinyl floor coverings, wood flooring and ceramic tile, but soft subfloors like carpets must be removed. The subfloor will have to be even, flat, dry and level to within 0.1" in 6 feet.
Asphalt tile came on the market in the 1920s and was a very popular floor covering by the 1950s. Asphalt tiles are the true pioneers of the resilient tile field, and are the most economical of the different flooring types. Asphalt tile is available only in a limited number of colors and patterns, and requires a bit more maintenance than do the others. Another disadvantage is that it is considerably more rigid, so it tends to be more susceptible to cracking. However, asphalt tile can be the perfect choice for utility areas or for other places demanding an economical floor. While not as abuse resistant as modern day materials, asphalt tiles are more durable than linoleum, and are easily cleaned with ordinary soap and water. They usually come in 9” x 9” x 1/8” thick tiles.
Vinyl made its debut in 1933 at the Chicago Century of Progress Exposition when the first vinyl composition tile was introduced. This composition was a mixture of polyvinyl chloride polymers, asbestos, limestone, other binders, and pigment. The addition of asbestos fibers gave the tiles excellent abrasion resistance, strength, and durability, as well as added flexibility. The vinyl-asbestos tile, VAT, was also highly resistant to moisture, oil and grease, heat, and a variety of chemicals. Because of the scarcity of materials during the war years, vinyl-asbestos floor tile was not widely marketed. However, with the increase in construction that occurred in the late 1940's, architects and builders soon found a large market for the very versatile and affordable floor covering. Asbestos fibers are firmly encapsulated in the mixture and pose no health risk unless the tiles are deliberately broken and/or ground up, which can release the fibers into the air. There are many agencies that will test floor tile if questions arise, and suggest methods of dealing with the asbestos issue.
The vinyl flooring industry quickly realized the need to reformulate their products. Vinyl-composition tile, VCT, is a product that is made up of solid color vinyl chips, binders, and other products, and it is formed by heat and pressure. The most common product is the 12" x 12" x 1/8" thick tile, but sheet products and larger tiles are available. With an almost endless selection of colors, patterns, textures, and styles, VCT helped vinyl flooring manufacturers quickly regain the tile floor covering market. The reformulated product retained most of the attributes of tiles containing asbestos, although the abrasion resistance of VCT may be somewhat less; nevertheless, the advantages of the reformulated product far outweigh the disadvantages. Other features were introduced to the market such as a "no-wax" surface and cushion backing for a "softer feel underfoot".
In the last decade, market demands have encouraged manufacturers to develop specialized tiles such as slip resistant tile; embossed tile which imparts a tactile feel for the handicapped; and static control tiles for environmental conditions. With the variety of resilient tile flooring coverings available, each of them easy to install as well as capable of producing a durable, easy to maintain surface, it is easy to see why resilient tile flooring is second only to carpet as the most common floor covering in the United States.
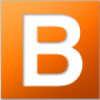
Buildipedia Staff
The Buildipedia research and writing staff consists of dozens of experienced professionals from many sectors of the industry, including architects, designers, contractors, and engineers.
Website: buildipedia.com/